Современная авиация постоянно сталкивается с проблемами роста конкуренции и повышением топливных затрат. Очевидным решением этих проблем является снижение веса конструкции за счет использования композиционных материалов
Современная авиация постоянно сталкивается с проблемами роста конкуренции и повышением топливных затрат. Очевидным решением этих проблем является снижение веса конструкции за счет использования композиционных материалов. В настоящее время процент содержания композитов в конструкциях современных самолетов составляет порядка 15%, но эта цифра является средней по всей отрасли. Бизнес-авиация традиционно консервативна в выборе конструкционных материалов. Однако и здесь случаются просветления.
Так собирают традиционные детали из алюминиевых сплавов
В бизнес-авиации применение композитов началось еще в прошлом веке. Однако новая технология преподнесла много проблем первопроходцам. А самыми известными на сегодняшний день «пластмассовыми» самолетами являются Beechcraft Premier I и Hawker 4000, разработанные компанией Raytheon Aircraft и переданные по наследству Hawker Beechcraft. Причем, если судьба меньшего собрата (Premier I) была более-менее удачной, то более крупный Hawker 4000 «хлебнул» новых технологий по полной программе – производитель 12 лет доводил самолет до серийного производства. Сейчас с композитами работает Bombardier в новом Learjet 85, но компания также сталкивается с проблемами в технологии производства композитного фюзеляжа. Из-за этого программа уже отстает от графика на полгода.
Вот и перспективные бизнес-джеты Dassault Falcon возможно будут иметь крылья, изготовленные из композитных материалов. Но фюзеляж, скорее всего, останется алюминиевым, при том, что в вышеприведенных самолетах как раз именно фюзеляж сделан из углеволокна. Об этом рассказал старший эксперт по технологии производства Dassault Филипп Вуте (Philippe Vautey), выступая на конференции, организованной Французской академией авиации и космонавтики в Париже в конце ноября 2012 года. На этом мероприятии он представил видение компании на перспективные модели бизнес-джетов Falcon, которые могут встать в строй через 4-8 лет. Однако эксперт не стал уточнять, относится ли это видение к засекреченному Falcon SMS.
При проектировании самолетов увеличение веса на 200 кг приравнивается к ухудшению аэродинамического качества на 2% и также увеличению на 2% удельного расхода топлива. В современной авиации это существенные величины, и поэтому инженеры-конструкторы стараются сэкономить вес конструкции всеми доступными способами. Однако снижение веса вступает в противоречие с прочностью, технологией и стоимостью производства и расходов на обслуживание воздушного судна. Поэтому, по словам Филиппа Вуте, всегда ищется компромисс, и конструкторы рассматривают три основных вопроса при выборе между композитами и металлом: Сколько веса можно сбросить, если это возможно? Каковы будут затраты на техобслуживание? Каковы будут издержки при производстве?
Причем эти проблемы решают конструкторы всех авиастроительных компаний, однако ответы могут быть разными, в зависимости от класса разрабатываемого самолета, как например в Airbus и Dassault.
А так "наматывали" фюзеляж Hawker 4000
«В сегменте бизнес-авиации цена является более сильным аргументом при принятии решения о покупке, чем на рынке коммерческих авиалайнеров», - подчеркивает эксперт Dassault. «Для операторов затраты на техническое обслуживание планера и общие прямые эксплуатационные расходы являются очень важными. Именно поэтому в бизнес-авиации труднее оправдать более высокую стоимость композитных деталей по сравнению с алюминиевыми. Несмотря на то, что композитные элементы конструкции имеют преимущества перед традиционными металлическими деталями по усталостным характеристикам и защите от коррозии, из-за того, что бизнес-джеты летают значительно меньшее коммерческих лайнеров, эти преимущества не играют существенной роли».
Как пример, Филипп Вуте приводит периодичность ремонтов на бизнес-джетах Falcon: первый капитальный ремонт на французском самолете должен проводиться через 12000 летных часов и при среднем ежегодном налете в 500 часов, первый покупатель обычно продает самолет прежде, чем он достигнет этого порога.
Однако, среди заказчиков зачастую бытует мнение, что если они покупают современный частный самолет, то он должен быть построен на основе последних технологий и достижений. Филипп Вуте рассказал историю о состоятельном человеке, который на церемонии получения своего нового бизнес-джета Falcon сказал: «Я очень доволен своим новым Falcon и его крылом, сделанным из углеволокна», и при этом постучал по алюминиевому крылу самолета. На такой прокол клиента скорее всего повлиял тот факт, что его спортивный автомобиль имел множество деталей из углепластика, и он, наверное, слышал о применении этого материала в Airbus и Boeing, поэтому и решил, что уж его бизнес-джет точно оснащен таким крылом. Филиппу Вуте пришлось объяснить новому владельцу, что Dassault сделал лучший выбор для крыла его Falcon – это металл.
Но такая ситуация была до настоящего времени, и скоро она может измениться. Dassault провела исследование, которое показало, что углепластиковый кессон крыла может быть на 15-20% легче, чем металлический аналог, и это сэкономит нескольких сотен килограммов. Принимая во внимание материалы и процессы, которые сегодня находятся на 5-м уровне технологической готовности (TRL 5 – демонстрации технологии), такая экономия веса может быть достигнута без увеличения издержек производства. Однако Филипп Вуте предупреждает, что для крыльев еще должны быть решены вопросы оптимизации конструкции, автоматизации процессов и долговечности деталей.
Но для фюзеляжа пока основным конструкционным материалом остается металл. В связи с относительно низким уровнем напряжений в этом элементе самолета, листы из алюминиевого сплава, которые используются для обшивки, могут быть тонкими, около одного миллиметра. Попытка сократить вес путем перехода на углепластик могла бы способствовать еще большему утончению обшивки, но не имеет никакого смысла из-за других ограничений, таких как качество поверхности, защита от удара молнии и системы заземления.
Сейчас разрабатываются новые сплавы, такие как алюминий-магний-литиевые, которые будут иметь низкую плотность, и их применение позволит на каждом фюзеляже экономить 5-8% от веса конструкции, что составит несколько десятков килограммов. А увеличение стоимости материалов может быть компенсировано заменой клепки сваркой трением, которую Dassault собирается применять в производстве.
В производстве металлических крыльев бизнес-джетов Falcon компания также может снизит вес конструкции, применив новые, но уже испытанные сплавы, такие как алюминий-медно-литиевые, которые дают небольшой выигрыш в плотности, однако имеют высокие прочностные характеристики. По словам Филиппа Вуте, Dassault еще долго будет использовать алюминиевые сплавы в конструкции своих самолетов. И одна из причин этого – недавние инвестиции в размере € 12 млн. ($ 15,6 млн.) в металлообрабатывающее оборудование завода в Секлин, северная Франция.
И напоследок, эксперт Dassault назвал еще один возможный способ снижения веса конструкции самолета – это «замена» килограммов на сроки техобслуживания. То есть, производитель рассматривает возможность сокращения срока до первого капитального ремонта, который сейчас наступает через 12000 летных часов. Выбор некоторых материалов может быть смещен в сторону «менее прочных, но более легких», что конечно приведет к более частому обслуживанию и тщательному контролю, но позволит сэкономить десятки килограммов в весе конструкции. Однако этот путь рассматривается как гипотетически возможный, но не единственный.
Композиционные технологии в авиации на нынешнем этапе развития более подходят к самолетам небольшого размера. И таких моделей очень много среди поршневых самолетов для личного применения. Однако отработка технологии и выпуск более крупных воздушных судов (например, Boeing 787) позволяет надеяться на применение таких прогрессивных материалов в «консервативной» бизнес-авиации.
Источник: BizavWeek
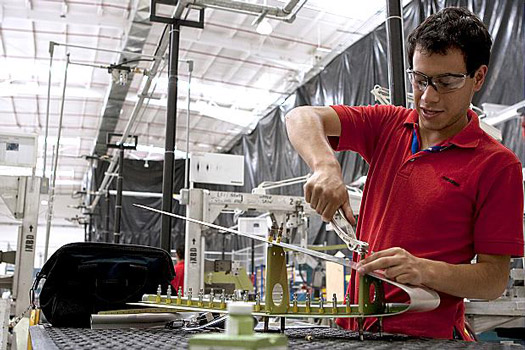
Так собирают традиционные детали из алюминиевых сплавов
В бизнес-авиации применение композитов началось еще в прошлом веке. Однако новая технология преподнесла много проблем первопроходцам. А самыми известными на сегодняшний день «пластмассовыми» самолетами являются Beechcraft Premier I и Hawker 4000, разработанные компанией Raytheon Aircraft и переданные по наследству Hawker Beechcraft. Причем, если судьба меньшего собрата (Premier I) была более-менее удачной, то более крупный Hawker 4000 «хлебнул» новых технологий по полной программе – производитель 12 лет доводил самолет до серийного производства. Сейчас с композитами работает Bombardier в новом Learjet 85, но компания также сталкивается с проблемами в технологии производства композитного фюзеляжа. Из-за этого программа уже отстает от графика на полгода.
Вот и перспективные бизнес-джеты Dassault Falcon возможно будут иметь крылья, изготовленные из композитных материалов. Но фюзеляж, скорее всего, останется алюминиевым, при том, что в вышеприведенных самолетах как раз именно фюзеляж сделан из углеволокна. Об этом рассказал старший эксперт по технологии производства Dassault Филипп Вуте (Philippe Vautey), выступая на конференции, организованной Французской академией авиации и космонавтики в Париже в конце ноября 2012 года. На этом мероприятии он представил видение компании на перспективные модели бизнес-джетов Falcon, которые могут встать в строй через 4-8 лет. Однако эксперт не стал уточнять, относится ли это видение к засекреченному Falcon SMS.
При проектировании самолетов увеличение веса на 200 кг приравнивается к ухудшению аэродинамического качества на 2% и также увеличению на 2% удельного расхода топлива. В современной авиации это существенные величины, и поэтому инженеры-конструкторы стараются сэкономить вес конструкции всеми доступными способами. Однако снижение веса вступает в противоречие с прочностью, технологией и стоимостью производства и расходов на обслуживание воздушного судна. Поэтому, по словам Филиппа Вуте, всегда ищется компромисс, и конструкторы рассматривают три основных вопроса при выборе между композитами и металлом: Сколько веса можно сбросить, если это возможно? Каковы будут затраты на техобслуживание? Каковы будут издержки при производстве?
Причем эти проблемы решают конструкторы всех авиастроительных компаний, однако ответы могут быть разными, в зависимости от класса разрабатываемого самолета, как например в Airbus и Dassault.
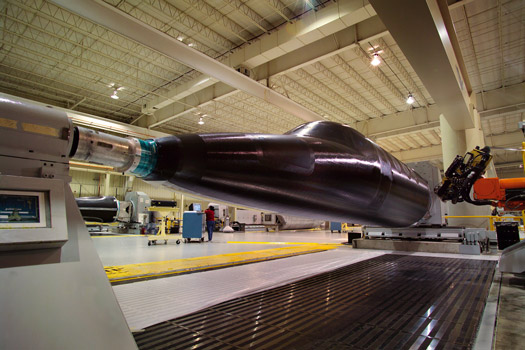
А так "наматывали" фюзеляж Hawker 4000
«В сегменте бизнес-авиации цена является более сильным аргументом при принятии решения о покупке, чем на рынке коммерческих авиалайнеров», - подчеркивает эксперт Dassault. «Для операторов затраты на техническое обслуживание планера и общие прямые эксплуатационные расходы являются очень важными. Именно поэтому в бизнес-авиации труднее оправдать более высокую стоимость композитных деталей по сравнению с алюминиевыми. Несмотря на то, что композитные элементы конструкции имеют преимущества перед традиционными металлическими деталями по усталостным характеристикам и защите от коррозии, из-за того, что бизнес-джеты летают значительно меньшее коммерческих лайнеров, эти преимущества не играют существенной роли».
Как пример, Филипп Вуте приводит периодичность ремонтов на бизнес-джетах Falcon: первый капитальный ремонт на французском самолете должен проводиться через 12000 летных часов и при среднем ежегодном налете в 500 часов, первый покупатель обычно продает самолет прежде, чем он достигнет этого порога.
Однако, среди заказчиков зачастую бытует мнение, что если они покупают современный частный самолет, то он должен быть построен на основе последних технологий и достижений. Филипп Вуте рассказал историю о состоятельном человеке, который на церемонии получения своего нового бизнес-джета Falcon сказал: «Я очень доволен своим новым Falcon и его крылом, сделанным из углеволокна», и при этом постучал по алюминиевому крылу самолета. На такой прокол клиента скорее всего повлиял тот факт, что его спортивный автомобиль имел множество деталей из углепластика, и он, наверное, слышал о применении этого материала в Airbus и Boeing, поэтому и решил, что уж его бизнес-джет точно оснащен таким крылом. Филиппу Вуте пришлось объяснить новому владельцу, что Dassault сделал лучший выбор для крыла его Falcon – это металл.
Но такая ситуация была до настоящего времени, и скоро она может измениться. Dassault провела исследование, которое показало, что углепластиковый кессон крыла может быть на 15-20% легче, чем металлический аналог, и это сэкономит нескольких сотен килограммов. Принимая во внимание материалы и процессы, которые сегодня находятся на 5-м уровне технологической готовности (TRL 5 – демонстрации технологии), такая экономия веса может быть достигнута без увеличения издержек производства. Однако Филипп Вуте предупреждает, что для крыльев еще должны быть решены вопросы оптимизации конструкции, автоматизации процессов и долговечности деталей.
Но для фюзеляжа пока основным конструкционным материалом остается металл. В связи с относительно низким уровнем напряжений в этом элементе самолета, листы из алюминиевого сплава, которые используются для обшивки, могут быть тонкими, около одного миллиметра. Попытка сократить вес путем перехода на углепластик могла бы способствовать еще большему утончению обшивки, но не имеет никакого смысла из-за других ограничений, таких как качество поверхности, защита от удара молнии и системы заземления.
Сейчас разрабатываются новые сплавы, такие как алюминий-магний-литиевые, которые будут иметь низкую плотность, и их применение позволит на каждом фюзеляже экономить 5-8% от веса конструкции, что составит несколько десятков килограммов. А увеличение стоимости материалов может быть компенсировано заменой клепки сваркой трением, которую Dassault собирается применять в производстве.
В производстве металлических крыльев бизнес-джетов Falcon компания также может снизит вес конструкции, применив новые, но уже испытанные сплавы, такие как алюминий-медно-литиевые, которые дают небольшой выигрыш в плотности, однако имеют высокие прочностные характеристики. По словам Филиппа Вуте, Dassault еще долго будет использовать алюминиевые сплавы в конструкции своих самолетов. И одна из причин этого – недавние инвестиции в размере € 12 млн. ($ 15,6 млн.) в металлообрабатывающее оборудование завода в Секлин, северная Франция.
И напоследок, эксперт Dassault назвал еще один возможный способ снижения веса конструкции самолета – это «замена» килограммов на сроки техобслуживания. То есть, производитель рассматривает возможность сокращения срока до первого капитального ремонта, который сейчас наступает через 12000 летных часов. Выбор некоторых материалов может быть смещен в сторону «менее прочных, но более легких», что конечно приведет к более частому обслуживанию и тщательному контролю, но позволит сэкономить десятки килограммов в весе конструкции. Однако этот путь рассматривается как гипотетически возможный, но не единственный.
Композиционные технологии в авиации на нынешнем этапе развития более подходят к самолетам небольшого размера. И таких моделей очень много среди поршневых самолетов для личного применения. Однако отработка технологии и выпуск более крупных воздушных судов (например, Boeing 787) позволяет надеяться на применение таких прогрессивных материалов в «консервативной» бизнес-авиации.
Источник: BizavWeek